Turns out that refitting a track isn’t that hard if you have the proper tools. Proper tools in this instance equaling crowbars, sledge, socket set...... and a 6 ton excavator with a driver who’s been using it long enough that it’s an extension of his hand.
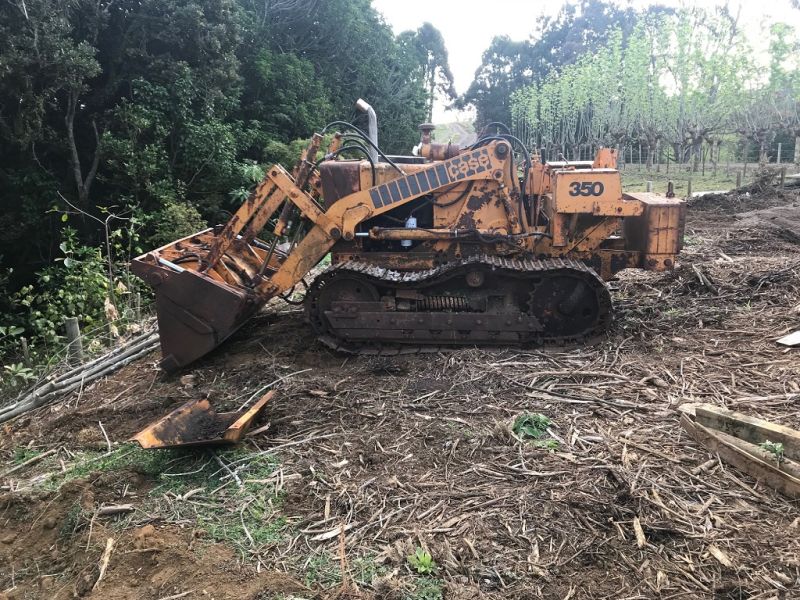
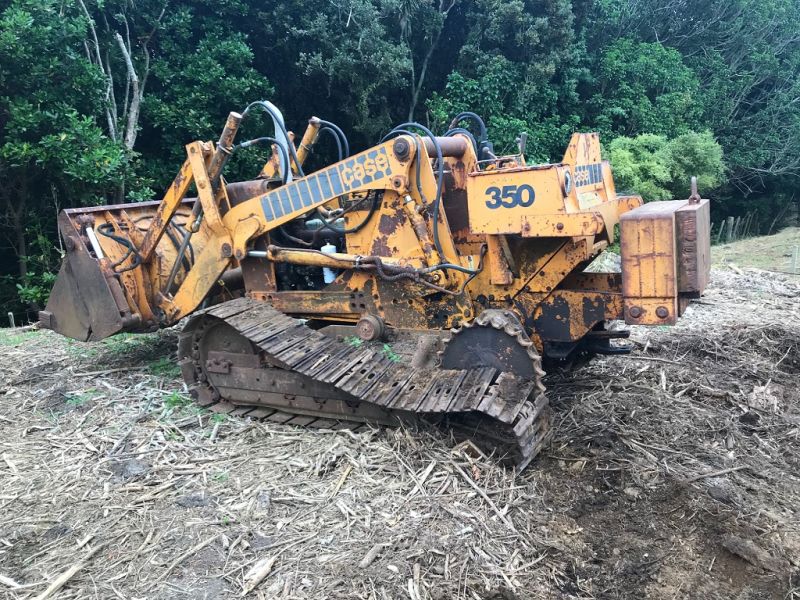
Method:
- Fire him up and use his bucket to lift his nose off the ground. Remove track from front idler wheel.
- Compress track tensioner by removing the preload cylinder, removing the grease nipple from it, then standing on it to extrude the grease out and compress it. This took about 2 hours but it’s a 15 minute job now I know how to do it
- Refit cylinder and knock nose wheel back to minimum extension with sledge hammer
- Drop his nose back on the ground and use chains on excavator bucket to lift track onto rear (drive) wheel
- Raise his bucket to lift his tail a little, stick him in gear and let him pull out the slack underneath
- Lift his nose off the ground again. Use chains on excavator, crowbars and some cussing to lift track partly over nose wheel
- Drive him forward against his bucket wedged into the ground, while pushing sideways on the track with the excavator bucket, to get track all the way round both main wheels
- Push him sideways with excavator till he comes off the ground on the problem side, then bash bottom of track with sledgehammer to get it back over the rollers
- Drop him back on the ground and reverse him a few feet to settle everything in place.
- Job done. Or at least it will be once I go buy a grease gun to re-pressurise the track tensioner.
Advertisement
Having access to an excavator isn’t regular thing, so I better not lose the track again - I’m not sure refitting it’d even be possible for one person without heavy equipment.
As is standard for Project Make Casey Great Again, it was a “one step forward, one step back” day though - blew a hydraulic line during the process, so now I’ve got two leaks in the bucket system :-(.